A discussion forum on Marine Safety, Recreational Boating Safety, and waterways managment as we work together to protect maritime commerce and mobility, the marine environment, and safety of life at sea.
Tuesday, March 30, 2010
Upcoming in Proceedings
• Rulemaking 101
• Interagency interaction
• Supporting analysis
• Public participation
Summer 2010: Maritime Domain Awareness
• Transforming MDA policy
• Transforming MDA capabilities
• Transforming MDA through technology
Fall 2010: Recreational Boating Safety (RBS)
• RBS program synopsis
• State RBS involvement
• RBS partners
• Manufacturing standards
• USCG Auxiliary
• Small vessel security
Your Opinion
• What do you want to read in Proceedings?
• What area under the Coast Guard’s marine safety, security, and environmental protection missions affects you most?
• What do you want to know more about?
Post a comment here or send us an e-mail at HQS-DG-NMCProceedings@uscg.mil.
Subscribe online at http://www.uscg.mil/proceedings/subscribe.asp.
Ask the MSSC—You have questions. We have answers from the USCG Marine Safety and Security Council.
How does the Coast Guard track medical conditions of non-licensed personnel?
Answered by the USCG Office of Vessel Activities.
Merchant mariner non-licensed personnel include two groups:
1. Qualified ratings such as able seaman, qualified member of the engineering department, and tankerman;
2. Entry-level positions such as ordinary seaman, wipers, and steward’s department personnel (food handlers).
The Coast Guard handles each of these groups differently.
Qualified ratings follow a process similar to licensed personnel. Qualified ratings are required to have physical examinations every five years. Compliance with this requirement is monitored through the application process. Applicants for original and renewal of credentials must submit a completed form CG 719K Merchant Mariner Physical Examination Report with their application. The CG-719K is completed by the medical professional who conducted the physical evaluation of the applicant. It documents a comprehensive review of the applicant’s medical and physical condition. The CG-719K is reviewed to flag any potential medical issues and a determination is made whether the mariner is physically qualified for a merchant mariner credential.
Entry-level applicants follow a similar but abbreviated process. They submit a different form, CG-719K/E Merchant Marine Certification of Fitness for Entry-Level Ratings. This form is shorter than that required of licensed personnel and qualified ratings. In the CG-719K/E the medical professional attests to the applicant’s ability to perform basic physical shipboard tasks. A full physical examination is not required. Entry-level applicants with limited service on non-seagoing vessels and/or on seagoing vessels of less than 200 gross register tons are not required to submit a physical exam of any type, nor are they required to demonstrate ability to perform basic physical shipboard tasks.
If the Coast Guard determines that a merchant mariner has a medical issue that may affect the mariner’s ability to perform his duties, the Coast Guard may still grant the credential. These waivers may require special conditions as simple as using and having spare eyeglasses aboard. In the case of medical conditions that are stable but have the potential to deteriorate over time, the medical waiver may include a stipulation that the mariner undergo periodic medical evaluations more frequently than the standard five years. All physical waivers require that the mariner report any change in the waived condition to the credential issuing authority within 30 days.
The Coast Guard monitors licensed personnel in the same manner, with the exception of pilots, who must submit a CG-719K annually.
Thursday, March 25, 2010
Lessons Learned—A ship capsizes while loading cargo—Part IV

Everyone on deck tumbled into the 30°F water of the Hudson River. A few seconds later, they were joined by all of the other crewmen except for three of the four who were down in the hold. Some were able to hold onto some part of the ship. Others were floating in the river.
It felt like 5°F with the wind chill factor. One multi-million-dollar generator was in the hold, and the other was on the bottom of the Hudson. Fuel oils and hydraulic fluids spilled into the river. The fuel would continue to seep into the river until the tank vents could be plugged.
The Response
The captain of a dredge working downriver made the distress call. Everybody on the wharf grabbed cell phones. In addition to the Coast Guard, the Marine Unit of Albany Fire and Rescue and a Good Samaritan vessel responded quickly. Meanwhile, workers on the wharf used a crane to pull people out of the water.
Tragically, all three of the men in the cargo hold either drowned or died of hypothermia. Everyone else was pulled out of the water alive. Five of these people had to be treated for injuries.
One real lesson learned was that there was no need for anyone to have been in the hold. Crewmen who weren’t directly engaged in the loading operation should not have been on the ship, especially considering that the crew had all night to secure the cargo for sea.
The Aftermath
The refloating operation took three weeks. The salvage company needed two barges with a large crane on each. In spite of the ship’s small size, this operation was not without difficulty. With the exception of the house and engine room, this little ship was all cargo hold, and all of it was full of water, since the ship was on its port side on the bottom.
The group planned to get the hatch covers back on as quickly as possible so the hold could be dewatered. The hatch covers were the type put on in sections, using the ship’s derricks. This created greater difficulty, as the hatch-cover sections were hollow and had a tendency to float. With cutting torches, the salvage crew burned holes in the sections so they could fill with water and sink as they were manhandled into place. Fortunately, the pumps discharged at a faster rate than the inflow of river water, and the dewatering operation was a success.
With divers in the water, boats were able to get wire slings around both of the derricks’ masts and the two cranes (aboard the barges) took a strain. The ship maintained a severe 20° list through the remainder of the dewatering operation.
Finally, the ship floated upright. There was a coating of oil everywhere and people had to be extremely cautious with every step. The two generators were recovered, and the barge cranes were able to get them onto the wharf.
In May of 2004, the Albany Maritime Ministry held a memorial service for the three men who perished. A ceremonial gravestone with their names and the name of their ship was placed in a park adjacent to the Port of Albany.
For more information:
Full article is available at www.uscg.mil/proceedings. Click on “archives” and “2008 Volume 65, Number 2” (Summer 2008).
Subscribe online at http://www.uscg.mil/proceedings/subscribe.asp.
Direct requests for print copies of this edition to: HQS-DG-NMCProceedings@uscg.mil.
Tuesday, March 23, 2010
Lessons Learned—A ship capsizes while loading cargo—Part III

The First Lift
The first load went smoothly. The cranes were slewed out and positioned over the wharf and swing ballast was loaded into tanks on the inboard side. The combined effect of the weight of the booms and the ballast listed the ship slightly toward the wharf, as desired.
At this point, someone would have checked the stability pontoon, since it would be effective only if the list did not exceed 2.5°. While someone checked on the pontoon, people on the wharf hooked the generator to the cargo falls, which took a few minutes due to the size and weight of the lifting hardware.
When everyone was in position, the winch operator took a strain. The captain also gave the order to begin filling ballast tanks on the outboard side before the list could get to a point that the pontoon could come out of position and lose its effectiveness. If it had come out of position, the ship might have capsized onto the wharf.
Reaching the point of full tension on the falls, the crew started to slew the booms inboard, exercising caution to ensure the load didn’t get ahead of the swing ballast. From time to time, the movement of the cargo was stopped to allow the swing ballast to catch up to the cargo.
Eventually, the two large port-side ballast tanks were filled and the generator was positioned over the hatch, three meters to port of the ship’s centerline. From here it took a few more minutes to lower it down into the hold. Four crewmen down in the hold unhooked it and began securing it for sea. Unfortunately, they were still in the hold during the second lift.
The Second Lift
The second lift began the same way as the first, except for how the ship was ballasted. The swing ballast from the first lift remained in the large tanks on the port side. Using that setup, the captain could plan on discharging the starboard side swing ballast while the load was slewed aboard.
The derricks were slewed out so the heads of the booms were over the wharf with the 308-ton generator. The boom heads were now 13 meters to starboard from the centerline, which caused a list to starboard. Additionally, the captain had one large starboard-side ballast tank filled to cause a maximum safe list before taking a strain on the cargo runners.
The generator was hooked up with hardware weighing over 20 tons. Meanwhile, the captain and cargo superintendent checked the stability pontoon to ensure the crewmen operating the winches and pumps were in position and ready. Additionally, there were four men down in the hold securing the smaller generator for sea, and a few others were in their staterooms or in the galley.
As the runners took a strain, ballast was discharged from the large starboard side tanks and the empty ballast tanks on the port side were filled. All of this happened faster than it should have. By the time there was full tension on the cargo runners, all port tanks were full and both of the large starboard tanks were empty.
The First Mistake
This meant that there was no place to put ballast on the port side in case there was a need for it. The port side had no “reserve ballast capacity,” a phrase coined by the Coast Guard’s technical advisor to the investigating officer.
With full tension on the cargo runners, the captain had the idea that he could discharge port-side ballast while slewing in the derricks to bring the generator aboard and prevent the ship from listing toward its port side.

This would not have been a problem if the stability pontoon had remained in position. The derricks were slewed in faster than they should have been; but the real mistake was that no crewmember was stationed to observe the pontoon for this second lift.
At some point before the port-side ballast discharge began, the pontoon became submerged. This meant that the ship, with its suspended load, was unstable but the captain didn’t realize it. The suspended weight was hanging slightly to starboard and all the port-side ballast tanks were full. At that point, the captain realized the ship was listing to port.
The best course of corrective action would have been to ballast. Stability teachings dictate ballasting an unstable ship first on the low side, so the ship can’t flop from a port list to a starboard list and capsize. However, since all the port-side ballast tanks were still nearly full, the alternative should have been to ballast on the starboard side; that is, ballast anywhere possible to make the ship less unstable.
The Third Mistake
Unfortunately the captain didn’t realize the condition of instability caused by the submerged pontoon and continued discharging port-side ballast in hope of alleviating the port list. The center of gravity got higher with every ton of ballast discharged, and the situation became more dangerous.
Then, the inevitable happened—the ship capsized (to its port side, away from the wharf) with unnecessary personnel aboard. In addition to the loading crew, there were four down in the hold, a cook in the galley, and other crewmen were in their staterooms.
In part IV we will explore the aftermath.
For more information:
Full article is available at www.uscg.mil/proceedings. Click on “archives” and "2008 Volume 65, Number 2" (Summer 2008).
Subscribe online at http://www.uscg.mil/proceedings/subscribe.asp.
Direct requests for print copies of this edition to: HQS-DG-NMCProceedings@uscg.mil.
Thursday, March 18, 2010
Lessons Learned—A ship capsizes while loading cargo—Part II

Stability in Action
Any student of stability needs to consider the vertical location of the weight of a piece of cargo. The weight is either in the hold, a few feet above or below the ship’s center of gravity, or the weight is “acting from” a point (such as the head of the cargo boom) that can be 100 feet above where it would be when the piece is down in the cargo hold.
In the rocking chair example from Part I, if you hung a 15-lb. weight from the horizontal top piece of the chair, then moved that weight onto the seat of the chair, the center of gravity would have shifted during this operation.
A stability pontoon is a floating vessel that makes a 300-ton lift and load possible. For a ship this size, the pontoon is approximately 50 meters in length and floats alongside the outboard side of the ship. The pontoon increases the ship’s “effective breadth”; the wider a vessel, the more stable it is. This ship used a stability pontoon on the outboard side that day.
The “Typical” Lift Procedure
After connecting the hardware (slings and lifting beam) to the cargo falls, the first step in lifting a weight of this magnitude is to take a slight strain (50 tons, in this case) on the falls using the winches. The strain is judged by the dynamometer gauges and the list of the ship. A ship this small takes on a list of 2.5 degrees or so with two cranes over the wharf and a 50-ton strain on the falls.
Next, the ballast tanks on the opposite (outboard) side of the ship are filled with water. If the ship is moored starboard side to the wharf (as this ship was), the port side ballast tanks are filled with river water to help bring the load across from starboard to port. As they’re filling, tension on the falls increases. The goal is to have less wear and tear on the winches and a smoother, safer loading operation. The ship’s center of gravity rises as the falls gather more tension from the cargo’s weight.
Depending on the loading plan, ballast water is either pumped from the inboard side to the outboard side, or the tanks on the outboard side are filled from the water in which the ship is floating. The idea of ballasting, by itself, lowers the ship’s center of gravity. The ballast water in this case is referred to as “swing ballast” because its primary purpose is to help swing the load aboard.
The applied ballast also has a tendency to lower the center of gravity a foot or two, but that helps to balance out the suspended load, which has a tendency to raise the center of gravity a few feet.
This is a very slow operation for two reasons: it takes time to fill ballast tanks, and it takes time for cargo to be lifted. Both operations take place simultaneously. Although the ballast tanks on a heavy-lift ship can be filled at a rate of over 200 tons per hour, the speed is determined by the time it takes to slew the cranes inboard.
When everyone is in position and ready, the winch operator takes a strain. The captain simultaneously gives the order to begin filling ballast tanks on the outboard side before the list gets to a point that the pontoon comes out of position and loses its effectiveness. If it does, the ship could capsize to starboard onto the wharf.
Reaching the point of full tension on the falls, the booms will get slewed inboard. Everyone exercises caution to ensure the cargo load doesn’t get ahead of the swing ballast. From time to time the cargo movement stops and the brakes are set to allow the ballast to catch up to the load. The idea is to do as much as possible with swing ballast to ease the operation of the booms.
In part III, we will examine the ways this lift differed from this typical example.
For more information:
Full article is available at www.uscg.mil/proceedings. Click on “archives” and "2008 Volume 65, Number 2" (Summer 2008).
Subscribe online at http://www.uscg.mil/proceedings/subscribe.asp.
Direct requests for print copies of this edition to: HQS-DG-NMCProceedings@uscg.mil.
Tuesday, March 16, 2010
Lessons Learned—A Ship Capsizes While Loading Cargo—Part I
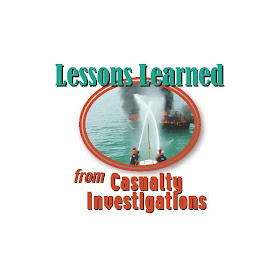
Lessons learned from USCG marine casualty reports are regularly featured in Proceedings of the Marine Safety & Security Council magazine. These articles explore marine incidents and the causal factors, outline the subsequent U.S. Coast Guard marine casualty investigations, and describe the lessons learned as a result.
It is important to note that lives were lost in some of the marine casualties we present. Out of respect for the deceased, their families, and surviving crewmembers, we do not mention the name of any person involved.
On December 9, 2003, the 289-foot heavy-lift freighter Stellamare capsized and sank in Albany, N.Y., while loading a 308-metric-ton generator. This marine casualty, which resulted in the deaths of three of the ship’s crew, was caused by improper ballasting and the speed of cargo handling.
The operation of a small heavy-lift ship is highly specialized. This is a ship less than 300 feet long, whose deadweight tonnage is only 2,760 metric tons, with cargo gear capable of lifting a total of 360 tons. This ship was fitted with two heavy-lift derricks, each of which was rated for a safe working load of 180 metric tons, so a combined load of 360 tons was permissible.
Two generators were to be loaded aboard this ship that day. One weighed 308 metric tons, the other 234 metric tons. During operations, the smaller generator was loaded as planned. It was loaded first, onto what had been an empty ship, to make the ship more stable in preparation for the heavier generator.
Stability: An Illustration
It’s important to understand what is meant by “stability.” There are three states of stability: stable, neutral, and unstable. Think of a child in a rocking chair. The chair rocking forward and backward is analogous to a ship rolling to starboard and port. If the child is sitting, the chair is very stable and can be rocked back and forth, but won’t topple over forward or backward because the center of gravity of the child and chair combination is down low.
But what if the child decides to kneel? Then the chair will be in “neutral” equilibrium. If the child leans forward, there is neither a tendency for the chair to return to the upright position nor a tendency for the chair to topple. The chair will stay where the child positions himself while kneeling.
If the child stands up in the chair, the center of gravity of the child and chair combination is now too high—unstable equilibrium. If the standing child moves too far forward or backwards, the chair can topple.
Let’s continue our example. How can we make the chair more stable so the child can’t upset it by standing? One way would be to fasten bricks to the underside of the chair, which would add weight below the desired center of gravity. In other words, we could “ballast” the rocking chair. We could also lengthen the chair’s rockers, which would be analogous to making a ship wider.
In Part II, we will examine how these principles were used in the failed loading operation.
For more information:
Full article is available at www.uscg.mil/proceedings. Click on “archives” and "2008 Volume 65, Number 2" (Summer 2008).
Subscribe online at http://www.uscg.mil/proceedings/subscribe.asp.
Direct requests for print copies of this edition to: HQS-DG-NMCProceedings@uscg.mil.
Thursday, March 11, 2010
Going Green Reaps Rewards—the Coast Guard recognizes industry’s marine environmental protection efforts

RADM William “Mike” Benkert (see sketch) was considered by many to be the father of the U.S. Coast Guard’s marine safety program. While serving as the office chief of marine environmental systems, RADM Benkert initiated many of the programs we have in the prevention department today.
RADM William M. Benkert Award
This prestigious award recognizes outstanding achievements that extend far beyond mere compliance with industrial and regulatory standards. More than just a symbol of excellence, the award provides an avenue for creative exchanges of ideas and innovations that benefit both the industry and the public.
The U.S. Coast Guard is proud to partner with the American Petroleum Institute (API) in this program. The API has hosted the Benkert Award presentations during the last several award ceremonies and plans to continue its support of this award. API also provides senior event staff to assist with coordinating the Benkert Award presentations during its bi-annual tanker conference.
Although this event was originally geared toward the tanker community, it has expanded to include many important topics that cross all of the maritime industry.
Eligibility Details
Any marine transportation-related commercial organization owning, operating, or otherwise managing vessels, facilities, or fleeting areas; oil spill removal organizations; or other entities engaged in maritime operations are eligible to apply.
There are six categories in which a company may submit an application:
- Small business—vessel operations: less than 50 employees, headquarters in the United States
- Small business—facility operations: less than 50 employees, located in the United States, regulated under 33 CFR 126.05 or 33 CFR 154.105
- Special small business: less than 25 employees, located in the United States, maritime transportation-related entity
- Large business—vessel operations: 50 employees or greater, headquarters in the United States
- Large business—facility operations: 50 employees or greater, located in the United States, regulated under 33 CFR 126.05 or 33 CFR 154.105
- Foreign vessels: 250 full-time employees or greater, must have at least one foreign-flagged vessel over 1,600 gross tons and have conducted commerce at a U.S. port during the given award period
Organizations are evaluated on:
- environmental policies, objectives, and targets;
- pollution prevention, preparedness, response, and safety management;
- environmental outreach;
- partnerships;
- performance measures and results.
The award program has three levels of recognition—gold, silver, and bronze. If an organization exceeds all review criteria expectations, then an “Osprey” is awarded as the top prize. The program is capable of recognizing multiple recipients at any or all of these levels.
The application submission deadline is February 1 every “even” year. The selection process concludes April 1, and the informal notification is expected in May of the award year. Award presentations are held in June. For more information, go to http://homeport.uscg.mil/benkert.
For more information:
Full article and “Environmental Protection” edition of USCG Proceedings is available at http://www.uscg.mil/proceedings/Winter2008-09//.
Subscribe online at http://www.uscg.mil/proceedings/subscribe.asp.
Direct requests for print copies of this edition to: HQS-DG-NMCProceedings@uscg.mil.
Tuesday, March 9, 2010
Electronics Stewardship—“greening” the U.S. Coast Guard computer lifecycle
Like any other federal agency, the U.S. Coast Guard relies on an extensive network of computers to support all of its missions. Managing these computers in an environmentally sound manner is an important goal of the U.S. Coast Guard’s information technology (IT) community.
Environmentally Responsible IT Procurement
In procuring computer resources, the U.S. Coast Guard not only looks for the best value and performance in equipment; it also uses available federal resources to ensure its computers are environmentally friendly. An important tool used to procure computers is the electronic product environmental assessment tool™ (EPEAT).
This tool was sponsored by the Environmental Protection Agency and developed by a team comprised of industry experts that allows purchasers to compare electronic products based on environmental attributes, including reduction and elimination of environmentally sensitive materials, design for end of life, lifecycle extension, energy conservation, and packaging.
Environmentally Friendly Operations
Not only does the U.S. Coast Guard seek to minimize the environmental impact of its computer resources in procurement, but it also takes steps to operate its systems in a manner that is safe for the environment. The Coast Guard uses computers that are Energy Star®-qualified, which establishes efficiency requirements for all modes of a computer’s operation, enhancing energy savings.
In addition to conserving energy during the operation of its computer resources, the U.S. Coast Guard also maximizes the lifetime of these resources. We currently purchase a five-year warranty with all Coast Guard standard workstations. A longer computer lifetime leads to decreased waste production and saves money by decreasing the demand for new hardware.

After a computer has reached the end of its useful life, we take several important steps to ensure that all computers are disposed of in an environmentally friendly manner. One way is to transfer the equipment to other federal agencies that might be able to put the equipment to use.
Yet another option for computer disposal is to donate the computers to a learning program. In the USCG photo at left, 23 used computers were donated to Gakona Public School in Valdez, Alaska, courtesy of the local Coast Guard Marine Safety Office.
Finally, if the systems are not suitable for donation to either schools or other federal offices, the U.S. Coast Guard transfers the equipment to local defense reutilization marketing offices, where the equipment is sold, donated, or disposed of in accordance with federal environmental regulations.
For more information:
Full article and “Environmental Protection” edition of USCG Proceedings is available at http://www.uscg.mil/proceedings/Winter2008-09/.
Subscribe online at http://www.uscg.mil/proceedings/subscribe.asp.
Direct requests for print copies of this edition to: HQS-DG-NMCProceedings@uscg.mil.
Thursday, March 4, 2010
Creating a Culture of Preparedness—the International Oil Spill Conference
The International Oil Spill Conference (IOSC) is jointly sponsored by industry, government, and non-government organizations and is considered the Americas’ premier oil spill preparedness, prevention, and response conference. Since its inception in 1969, a total of 20 International Oil Spill Conferences have been held.
The IOSC is sponsored by the U.S. Coast Guard and some of its key maritime partners, including:
• the International Maritime Organization,
• the National Oceanic and Atmospheric Administration,
• the American Petroleum Institute,
• the Minerals Management Service,
• the United States Environmental Protection Agency,
• the International Petroleum Industry Environmental Conservation Association.
The U.S. Coast Guard provides critical leadership to the IOSC as co-chair of the general committee and chair of the program committee.
IOSC 2008
The theme of IOSC 2008 was “creating a culture of preparedness.” This theme served as a reminder to the response community that preparedness is a critical component of any oil spill response. More than 2,000 people from over 80 countries were in attendance for the technical sessions and viewed more than 250 exhibits.
The conference began with a series of short courses that ranged in topic from the basics of oil spill response to oil spill response techniques in the Arctic and the use of dispersants. These courses were followed by an on-water demonstration of oil spill response equipment.
The conference was officially convened by keynote speakers John Chatterton and Richie Kohler, co-hosts of The History Channel’s "Deep Sea Detectives" television show. They provided insight into the dangers involved in deep-sea diving and how crucial experience and training is to any operation, regardless of the profession.
In his closing speech, U.S. Coast Guard Commandant ADM Thad Allen highlighted the 40th anniversary of the National Oil and Hazardous Substance Contingency Plan and the importance of cooperation among all levels of government, the private sector, and non-government organizations.
Future of IOSC
The next IOSC will be held in 2011 and will be "going green," with IOSC 2011’s general committee specifically looking for venues that will reduce the conference’s environmental impact and analyzing its processes and products to eliminate waste.
For more information:
Full article and “Environmental Protection” edition of USCG Proceedings is available at http://www.uscg.mil/proceedings/Winter2008-09//.
Subscribe online at http://www.uscg.mil/proceedings/subscribe.asp.
Direct requests for print copies of this edition to: HQS-DG-NMCProceedings@uscg.mil.
Tuesday, March 2, 2010
Onshore Power Supply for Ships—reducing ship engine emissions
On the other hand, there are difficulties associated with high voltage, varying frequencies, and infrastructure costs that must be addressed in order to justify an onshore power supply installation.
System Requirements
A typical OPS system requires many components. At the very least, significant infrastructure is required for the cable handling system, switchgear, protective boxes, transformers, and power cables. Additionally, this equipment must not interfere with vessel cargo operations, cranes, or passenger transit, so proper location of the ship/shore interface is critical. The onshore power one-line electrical diagram shows a typical onshore power supply system.
The design of many modern vessels with high-voltage electrical distribution systems, such as those of 6,600 volts or 11,000 volts, enables more power to be transferred with less cable area than traditional 450V electrical systems. However, most of the vessels comprising the world’s fleets are 440V to 480V systems. The in-port power requirements for different types of vessels can vary substantially.
Benefits
The most notable benefit is reducing engine emissions in the port area. Once the infrastructure is set up, ships that make relatively frequent calls to particular ports can transition to onshore power supply as a matter of routine.
A secondary benefit of a secured plant is that maintenance and repairs can be facilitated on equipment that is not in operation. Also, the interval for receiving engine bunker fuel may be increased slightly as less ship fuel is used, and the relative cost of the energy provided by the shore facility may be favorable compared to the operating cost of ship engine/generator combinations.
Concerns
Cost. The cost of infrastructure, including electrical equipment such as transformers, switchgear, power cables, cable handling equipment, and associated support structures on the piers, is significant. Obviously, as the distance from the shore utility to the ships on the piers increases, the cost multiplies. Similarly, the cost increases as the number of onshore power supply locations increases.
Compatibility. The ship and shore frequencies must match within limits for OPS to even be considered. It generally requires a frequency converter for a 50-Hertz supply (shore) to work with 60-Hertz loads (ship), or vice versa. Frequency converters at the power levels required are an expensive addition to an already significant infrastructure.
Safety and quality of power. Standards must be agreed upon between ship operators and shore personnel as to safety procedures at a particular installation. Additionally, the minimum quality of electrical power required needs to be defined by the ship, such that safe disconnection of shore power can be initiated if the power quality deteriorates to a level where ship equipment may be damaged.
Standardization. Efforts to formally develop an international standard for OPS installations have been underway within the International Organization for Standardization since 2006.
For more information:
Full article and “Environmental Protection” edition of USCG Proceedings is available at http://www.uscg.mil/proceedings/Winter2008-09/.
Subscribe online at http://www.uscg.mil/proceedings/subscribe.asp.
Direct requests for print copies of this edition to: HQS-DG-NMCProceedings@uscg.mil.
Upcoming in Proceedings
• Rulemaking 101
• Interagency interaction
• Supporting analysis
• Public participation
Summer 2010: Maritime Domain Awareness
• Transforming MDA policy
• Transforming MDA capabilities
• Transforming MDA through technology
Your Opinion
• What do you want to read in Proceedings?
• What area under the Coast Guard’s marine safety, security, and environmental protection missions affects you most?
• What do you want to know more about?
Post a comment here or send us an e-mail at HQS-DG-NMCProceedings@uscg.mil.
Subscribe online at http://www.uscg.mil/proceedings/subscribe.asp.